What are the Manufacturing Processes of the Latest Thermal Resistors?
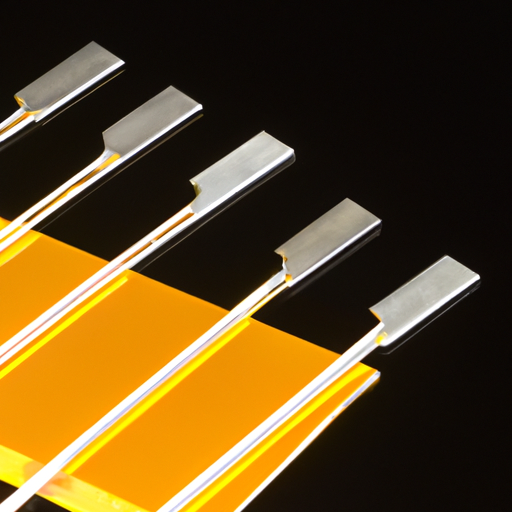
I. Introduction
Thermal resistors, commonly known as thermistors and resistance temperature detectors (RTDs), are essential components in a wide range of electronic applications. These devices are designed to measure temperature by correlating the resistance of the material to temperature changes. As technology has evolved, so too have the manufacturing processes and materials used in the production of thermal resistors, leading to enhanced performance, reliability, and versatility in various applications.
II. Types of Thermal Resistors
A. Thermistors
Thermistors are temperature-sensitive resistors that exhibit a significant change in resistance with temperature variations. They are categorized into two main types:
1. **NTC (Negative Temperature Coefficient)**: NTC thermistors decrease in resistance as temperature increases. They are widely used in temperature sensing and compensation applications.
2. **PTC (Positive Temperature Coefficient)**: PTC thermistors increase in resistance with rising temperature. They are often used in overcurrent protection and self-regulating heating applications.
B. RTDs (Resistance Temperature Detectors)
RTDs are temperature sensors that utilize the predictable change in electrical resistance of certain materials, typically pure metals like platinum, as temperature varies. They are known for their accuracy and stability, making them suitable for industrial applications.
C. Other Emerging Technologies
In addition to traditional thermistors and RTDs, new technologies are emerging, such as fiber optic temperature sensors and MEMS-based thermal sensors, which offer unique advantages in specific applications.
III. Materials Used in Thermal Resistor Manufacturing
A. Conductive Materials
1. **Metal Oxides for Thermistors**: NTC thermistors are often made from metal oxides, such as manganese, cobalt, and nickel oxides, which provide the necessary temperature sensitivity.
2. **Pure Metals for RTDs**: Platinum is the most common material used for RTDs due to its stable resistance-temperature characteristics and high melting point.
B. Insulating Materials
1. **Ceramics**: Ceramic materials are frequently used for thermistor substrates due to their excellent thermal stability and electrical insulation properties.
2. **Polymers**: Certain polymers are also used for insulation, particularly in applications requiring flexibility and lightweight materials.
C. Composite Materials and Their Advantages
Composite materials, which combine different materials to enhance performance, are increasingly being utilized in thermal resistor manufacturing. These composites can offer improved thermal conductivity, mechanical strength, and resistance to environmental factors.
IV. Manufacturing Processes
A. Design and Prototyping
The manufacturing process begins with design and prototyping. Engineers use computer-aided design (CAD) tools to create detailed models of thermal resistors. Simulation and modeling software help predict performance characteristics, allowing for optimization before physical production begins.
B. Material Preparation
1. **Sourcing Raw Materials**: Manufacturers must carefully source high-quality raw materials to ensure the performance and reliability of the final product.
2. **Material Processing Techniques**: Raw materials undergo various processing techniques, such as grinding, mixing, and sintering, to achieve the desired properties.
C. Fabrication Techniques
1. **Thick-Film Technology**: This method involves screen printing a paste of conductive materials onto a substrate, followed by firing to create a solid film. This technique is commonly used for thermistors.
2. **Thin-Film Technology**: In this process, a thin layer of conductive material is deposited onto a substrate using vacuum deposition techniques. Etching processes are then used to define the resistor pattern. Thin-film technology is often employed for RTDs due to its precision.
3. **Wire-Wound Techniques**: This traditional method involves winding a fine wire around a ceramic or glass core. The resistance is determined by the wire's length and diameter, making it suitable for high-precision applications.
D. Assembly and Packaging
Once the thermal resistors are fabricated, they undergo assembly and packaging. This includes mounting the resistors onto circuit boards or other substrates and encapsulating them in protective materials to ensure durability and reliability in various environments.
E. Quality Control and Testing
Quality control is a critical aspect of thermal resistor manufacturing. Various testing methods are employed, including:
1. **Electrical Testing**: Ensures that the resistors meet specified resistance values and performance characteristics.
2. **Environmental Testing**: Assesses the performance of thermal resistors under different environmental conditions, such as temperature extremes and humidity.
3. **Calibration Processes**: Calibration is performed to ensure accuracy and reliability in temperature measurements.
V. Innovations in Thermal Resistor Manufacturing
A. Advances in Materials Science
Recent advancements in materials science have led to the development of new conductive and insulating materials that enhance the performance of thermal resistors. These innovations contribute to improved sensitivity, stability, and durability.
B. Automation and Industry 4.0
The integration of automation and Industry 4.0 technologies in manufacturing processes has streamlined production, reduced costs, and improved quality control. Smart manufacturing systems enable real-time monitoring and data analysis, leading to more efficient operations.
C. Sustainable Manufacturing Practices
As environmental concerns grow, manufacturers are increasingly adopting sustainable practices. This includes using eco-friendly materials, reducing waste, and implementing energy-efficient processes.
D. Customization and Rapid Prototyping
The demand for customized thermal resistors has risen, prompting manufacturers to adopt rapid prototyping techniques. This allows for quick iterations and adjustments to meet specific customer requirements.
VI. Applications of Thermal Resistors
Thermal resistors play a crucial role in various industries, including:
A. Consumer Electronics
In consumer electronics, thermal resistors are used in devices such as smartphones, laptops, and home appliances to monitor and manage temperature, ensuring optimal performance and safety.
B. Automotive Industry
In the automotive sector, thermal resistors are essential for engine temperature monitoring, climate control systems, and battery management in electric vehicles.
C. Industrial Applications
Thermal resistors are widely used in industrial processes for temperature control, monitoring, and automation, contributing to efficiency and safety in manufacturing environments.
D. Medical Devices
In the medical field, thermal resistors are critical for temperature monitoring in devices such as incubators, patient monitoring systems, and diagnostic equipment.
E. Aerospace and Defense
In aerospace and defense applications, thermal resistors are used for environmental monitoring, ensuring the safety and reliability of equipment in extreme conditions.
VII. Future Trends in Thermal Resistor Manufacturing
A. Miniaturization and Integration
The trend towards miniaturization continues, with manufacturers developing smaller and more integrated thermal resistors that can fit into compact electronic devices without compromising performance.
B. Smart Thermal Resistors
The rise of the Internet of Things (IoT) has led to the development of smart thermal resistors that can communicate data wirelessly, enabling real-time monitoring and control in various applications.
C. Enhanced Performance Metrics
Future thermal resistors are expected to offer enhanced performance metrics, including faster response times, greater accuracy, and improved stability over a wider temperature range.
D. Global Market Trends and Forecasts
The global market for thermal resistors is projected to grow significantly, driven by advancements in technology and increasing demand across various industries. Manufacturers will need to adapt to changing market dynamics and customer needs.
VIII. Conclusion
The manufacturing processes of thermal resistors have evolved significantly, driven by advancements in materials science, technology, and market demands. As these components continue to play a vital role in various applications, ongoing research and development will be crucial in shaping the future of thermal resistor technology. The significance of these devices in ensuring safety, efficiency, and performance across industries cannot be overstated, making them an essential focus for manufacturers and researchers alike.
IX. References
A comprehensive list of academic journals, industry reports, and manufacturer specifications would typically follow to provide further reading and validation of the information presented in this blog post.
What are the Manufacturing Processes of the Latest Thermal Resistors?
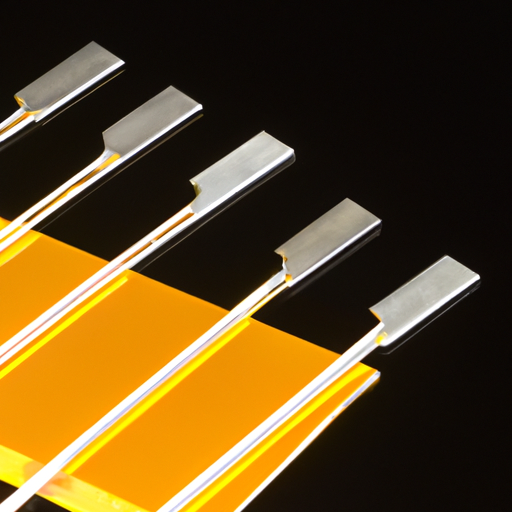
I. Introduction
Thermal resistors, commonly known as thermistors and resistance temperature detectors (RTDs), are essential components in a wide range of electronic applications. These devices are designed to measure temperature by correlating the resistance of the material to temperature changes. As technology has evolved, so too have the manufacturing processes and materials used in the production of thermal resistors, leading to enhanced performance, reliability, and versatility in various applications.
II. Types of Thermal Resistors
A. Thermistors
Thermistors are temperature-sensitive resistors that exhibit a significant change in resistance with temperature variations. They are categorized into two main types:
1. **NTC (Negative Temperature Coefficient)**: NTC thermistors decrease in resistance as temperature increases. They are widely used in temperature sensing and compensation applications.
2. **PTC (Positive Temperature Coefficient)**: PTC thermistors increase in resistance with rising temperature. They are often used in overcurrent protection and self-regulating heating applications.
B. RTDs (Resistance Temperature Detectors)
RTDs are temperature sensors that utilize the predictable change in electrical resistance of certain materials, typically pure metals like platinum, as temperature varies. They are known for their accuracy and stability, making them suitable for industrial applications.
C. Other Emerging Technologies
In addition to traditional thermistors and RTDs, new technologies are emerging, such as fiber optic temperature sensors and MEMS-based thermal sensors, which offer unique advantages in specific applications.
III. Materials Used in Thermal Resistor Manufacturing
A. Conductive Materials
1. **Metal Oxides for Thermistors**: NTC thermistors are often made from metal oxides, such as manganese, cobalt, and nickel oxides, which provide the necessary temperature sensitivity.
2. **Pure Metals for RTDs**: Platinum is the most common material used for RTDs due to its stable resistance-temperature characteristics and high melting point.
B. Insulating Materials
1. **Ceramics**: Ceramic materials are frequently used for thermistor substrates due to their excellent thermal stability and electrical insulation properties.
2. **Polymers**: Certain polymers are also used for insulation, particularly in applications requiring flexibility and lightweight materials.
C. Composite Materials and Their Advantages
Composite materials, which combine different materials to enhance performance, are increasingly being utilized in thermal resistor manufacturing. These composites can offer improved thermal conductivity, mechanical strength, and resistance to environmental factors.
IV. Manufacturing Processes
A. Design and Prototyping
The manufacturing process begins with design and prototyping. Engineers use computer-aided design (CAD) tools to create detailed models of thermal resistors. Simulation and modeling software help predict performance characteristics, allowing for optimization before physical production begins.
B. Material Preparation
1. **Sourcing Raw Materials**: Manufacturers must carefully source high-quality raw materials to ensure the performance and reliability of the final product.
2. **Material Processing Techniques**: Raw materials undergo various processing techniques, such as grinding, mixing, and sintering, to achieve the desired properties.
C. Fabrication Techniques
1. **Thick-Film Technology**: This method involves screen printing a paste of conductive materials onto a substrate, followed by firing to create a solid film. This technique is commonly used for thermistors.
2. **Thin-Film Technology**: In this process, a thin layer of conductive material is deposited onto a substrate using vacuum deposition techniques. Etching processes are then used to define the resistor pattern. Thin-film technology is often employed for RTDs due to its precision.
3. **Wire-Wound Techniques**: This traditional method involves winding a fine wire around a ceramic or glass core. The resistance is determined by the wire's length and diameter, making it suitable for high-precision applications.
D. Assembly and Packaging
Once the thermal resistors are fabricated, they undergo assembly and packaging. This includes mounting the resistors onto circuit boards or other substrates and encapsulating them in protective materials to ensure durability and reliability in various environments.
E. Quality Control and Testing
Quality control is a critical aspect of thermal resistor manufacturing. Various testing methods are employed, including:
1. **Electrical Testing**: Ensures that the resistors meet specified resistance values and performance characteristics.
2. **Environmental Testing**: Assesses the performance of thermal resistors under different environmental conditions, such as temperature extremes and humidity.
3. **Calibration Processes**: Calibration is performed to ensure accuracy and reliability in temperature measurements.
V. Innovations in Thermal Resistor Manufacturing
A. Advances in Materials Science
Recent advancements in materials science have led to the development of new conductive and insulating materials that enhance the performance of thermal resistors. These innovations contribute to improved sensitivity, stability, and durability.
B. Automation and Industry 4.0
The integration of automation and Industry 4.0 technologies in manufacturing processes has streamlined production, reduced costs, and improved quality control. Smart manufacturing systems enable real-time monitoring and data analysis, leading to more efficient operations.
C. Sustainable Manufacturing Practices
As environmental concerns grow, manufacturers are increasingly adopting sustainable practices. This includes using eco-friendly materials, reducing waste, and implementing energy-efficient processes.
D. Customization and Rapid Prototyping
The demand for customized thermal resistors has risen, prompting manufacturers to adopt rapid prototyping techniques. This allows for quick iterations and adjustments to meet specific customer requirements.
VI. Applications of Thermal Resistors
Thermal resistors play a crucial role in various industries, including:
A. Consumer Electronics
In consumer electronics, thermal resistors are used in devices such as smartphones, laptops, and home appliances to monitor and manage temperature, ensuring optimal performance and safety.
B. Automotive Industry
In the automotive sector, thermal resistors are essential for engine temperature monitoring, climate control systems, and battery management in electric vehicles.
C. Industrial Applications
Thermal resistors are widely used in industrial processes for temperature control, monitoring, and automation, contributing to efficiency and safety in manufacturing environments.
D. Medical Devices
In the medical field, thermal resistors are critical for temperature monitoring in devices such as incubators, patient monitoring systems, and diagnostic equipment.
E. Aerospace and Defense
In aerospace and defense applications, thermal resistors are used for environmental monitoring, ensuring the safety and reliability of equipment in extreme conditions.
VII. Future Trends in Thermal Resistor Manufacturing
A. Miniaturization and Integration
The trend towards miniaturization continues, with manufacturers developing smaller and more integrated thermal resistors that can fit into compact electronic devices without compromising performance.
B. Smart Thermal Resistors
The rise of the Internet of Things (IoT) has led to the development of smart thermal resistors that can communicate data wirelessly, enabling real-time monitoring and control in various applications.
C. Enhanced Performance Metrics
Future thermal resistors are expected to offer enhanced performance metrics, including faster response times, greater accuracy, and improved stability over a wider temperature range.
D. Global Market Trends and Forecasts
The global market for thermal resistors is projected to grow significantly, driven by advancements in technology and increasing demand across various industries. Manufacturers will need to adapt to changing market dynamics and customer needs.
VIII. Conclusion
The manufacturing processes of thermal resistors have evolved significantly, driven by advancements in materials science, technology, and market demands. As these components continue to play a vital role in various applications, ongoing research and development will be crucial in shaping the future of thermal resistor technology. The significance of these devices in ensuring safety, efficiency, and performance across industries cannot be overstated, making them an essential focus for manufacturers and researchers alike.
IX. References
A comprehensive list of academic journals, industry reports, and manufacturer specifications would typically follow to provide further reading and validation of the information presented in this blog post.