What are the Product Standards for the Function of Capacitors?
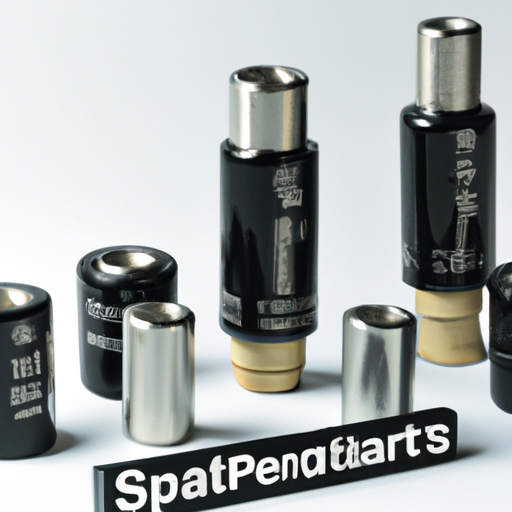
I. Introduction
Capacitors are fundamental components in electronic circuits, serving as energy storage devices that can release energy when needed. They play a crucial role in various applications, from smoothing out voltage fluctuations in power supplies to filtering signals in audio equipment. Given their importance, product standards for capacitors are essential to ensure their reliability, safety, and performance in diverse applications. This blog post will explore the product standards governing capacitors, the organizations involved in setting these standards, and the challenges and future trends in this field.
II. Understanding Capacitors
A. Basic Principles of Capacitance
Capacitance is defined as the ability of a component to store an electrical charge. It is measured in farads (F), with common subunits including microfarads (µF) and picofarads (pF). Capacitors consist of two conductive plates separated by an insulating material, known as a dielectric. When voltage is applied across the plates, an electric field is created, allowing the capacitor to store energy.
There are several types of capacitors, each with unique characteristics and applications:
1. **Ceramic Capacitors**: Known for their small size and stability, ceramic capacitors are widely used in high-frequency applications.
2. **Electrolytic Capacitors**: These capacitors offer high capacitance values and are commonly used in power supply circuits.
3. **Film Capacitors**: Made from thin plastic films, these capacitors are known for their reliability and are often used in audio and signal processing applications.
B. Applications of Capacitors in Various Industries
Capacitors find applications across multiple industries:
1. **Consumer Electronics**: In devices like smartphones and televisions, capacitors help manage power supply and signal processing.
2. **Automotive**: Capacitors are used in various automotive systems, including power management and audio systems.
3. **Industrial Machinery**: Capacitors play a vital role in motor starting and power factor correction in industrial settings.
4. **Renewable Energy Systems**: In solar inverters and wind turbines, capacitors help stabilize voltage and improve efficiency.
III. Regulatory Bodies and Standards Organizations
A. Overview of Key Organizations
Several organizations are responsible for establishing product standards for capacitors:
1. **International Electrotechnical Commission (IEC)**: The IEC develops international standards for electrical and electronic devices, including capacitors.
2. **Institute of Electrical and Electronics Engineers (IEEE)**: IEEE standards focus on electrical engineering and electronics, providing guidelines for capacitor performance and testing.
3. **Underwriters Laboratories (UL)**: UL is known for its safety certification, ensuring that capacitors meet safety standards for various applications.
4. **American National Standards Institute (ANSI)**: ANSI oversees the development of voluntary consensus standards for products, including capacitors.
B. Role of These Organizations in Setting Standards
These organizations collaborate with industry experts to create and update standards that ensure capacitors are safe, reliable, and effective. Their guidelines cover various aspects, including electrical performance, environmental impact, and safety requirements.
IV. Key Product Standards for Capacitors
A. Electrical Characteristics
1. **Capacitance Tolerance**: This standard specifies the allowable deviation from the nominal capacitance value. It ensures that capacitors perform within acceptable limits in circuits.
2. **Voltage Rating**: Capacitors must be rated for the maximum voltage they can handle without failure. Exceeding this rating can lead to catastrophic failure.
3. **Equivalent Series Resistance (ESR)**: ESR is a measure of the internal resistance of a capacitor, affecting its efficiency and heat generation. Lower ESR values are preferred for high-frequency applications.
4. **Leakage Current**: This standard measures the small amount of current that flows through a capacitor when it is not in use. High leakage current can indicate a failure or degradation of the capacitor.
B. Environmental and Mechanical Standards
1. **Temperature Range**: Capacitors must operate effectively within specified temperature ranges to ensure reliability in various environments.
2. **Humidity Resistance**: Capacitors are tested for their ability to withstand high humidity levels, which can affect their performance and longevity.
3. **Vibration and Shock Resistance**: Capacitors used in automotive and industrial applications must endure mechanical stress without failure.
C. Safety Standards
1. **Fire Safety**: Capacitors must meet fire safety standards to prevent ignition and ensure safe operation in electronic devices.
2. **RoHS Compliance**: The Restriction of Hazardous Substances (RoHS) directive limits the use of specific hazardous materials in electronic products, including capacitors.
3. **REACH Compliance**: The Registration, Evaluation, Authorisation, and Restriction of Chemicals (REACH) regulation ensures that chemicals used in capacitors are safe for human health and the environment.
V. Testing and Certification Processes
A. Overview of Testing Methods
1. **Electrical Testing**: This includes measuring capacitance, ESR, and leakage current to ensure that capacitors meet specified electrical characteristics.
2. **Environmental Testing**: Capacitors undergo tests to evaluate their performance under extreme temperature, humidity, and mechanical stress conditions.
3. **Mechanical Testing**: This involves assessing the physical integrity of capacitors under vibration and shock conditions.
B. Certification Process for Capacitors
1. **Pre-Certification Testing**: Before a capacitor can be certified, it undergoes rigorous testing to ensure it meets all relevant standards.
2. **Compliance Verification**: After testing, manufacturers must provide documentation demonstrating compliance with applicable standards.
3. **Ongoing Quality Assurance**: Manufacturers are required to maintain quality control processes to ensure that all produced capacitors continue to meet established standards.
VI. Challenges in Meeting Product Standards
A. Variability in Manufacturing Processes
Manufacturing processes can vary significantly between different manufacturers, leading to inconsistencies in capacitor performance. This variability can make it challenging to meet established standards consistently.
B. Evolving Technology and Standards
As technology advances, so do the standards governing capacitors. Manufacturers must stay updated on changes to ensure compliance, which can be resource-intensive.
C. Global Market Considerations
With a global market for capacitors, manufacturers must navigate different regulatory requirements in various countries, complicating the compliance process.
VII. Future Trends in Capacitor Standards
A. Innovations in Capacitor Technology
Emerging technologies, such as supercapacitors and organic capacitors, are changing the landscape of energy storage. Standards will need to evolve to accommodate these new technologies.
B. Anticipated Changes in Regulatory Standards
As environmental concerns grow, stricter regulations regarding the materials used in capacitors and their disposal are expected. Manufacturers will need to adapt to these changes to remain compliant.
C. The Impact of Sustainability on Capacitor Design and Standards
Sustainability is becoming a priority in capacitor design, with a focus on reducing environmental impact. Standards will likely evolve to promote the use of eco-friendly materials and manufacturing processes.
VIII. Conclusion
Product standards for capacitors are vital for ensuring their safety, reliability, and performance in electronic circuits. These standards, established by various regulatory bodies, cover electrical characteristics, environmental and mechanical requirements, and safety considerations. As technology evolves and the demand for sustainable practices increases, the standards governing capacitors will continue to adapt. Manufacturers must remain vigilant in meeting these standards to ensure their products are safe and effective in an ever-changing market.
IX. References
- International Electrotechnical Commission (IEC) Standards
- Institute of Electrical and Electronics Engineers (IEEE) Standards
- Underwriters Laboratories (UL) Certification Guidelines
- American National Standards Institute (ANSI) Standards
- RoHS and REACH Compliance Guidelines
This comprehensive overview of product standards for capacitors highlights their critical role in the electronics industry and the ongoing efforts to ensure their safety and effectiveness. As we look to the future, the evolution of these standards will be essential in meeting the challenges posed by new technologies and environmental considerations.
What are the Product Standards for the Function of Capacitors?
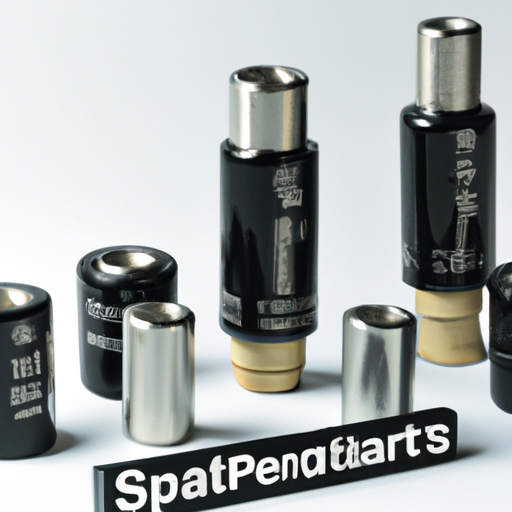
I. Introduction
Capacitors are fundamental components in electronic circuits, serving as energy storage devices that can release energy when needed. They play a crucial role in various applications, from smoothing out voltage fluctuations in power supplies to filtering signals in audio equipment. Given their importance, product standards for capacitors are essential to ensure their reliability, safety, and performance in diverse applications. This blog post will explore the product standards governing capacitors, the organizations involved in setting these standards, and the challenges and future trends in this field.
II. Understanding Capacitors
A. Basic Principles of Capacitance
Capacitance is defined as the ability of a component to store an electrical charge. It is measured in farads (F), with common subunits including microfarads (µF) and picofarads (pF). Capacitors consist of two conductive plates separated by an insulating material, known as a dielectric. When voltage is applied across the plates, an electric field is created, allowing the capacitor to store energy.
There are several types of capacitors, each with unique characteristics and applications:
1. **Ceramic Capacitors**: Known for their small size and stability, ceramic capacitors are widely used in high-frequency applications.
2. **Electrolytic Capacitors**: These capacitors offer high capacitance values and are commonly used in power supply circuits.
3. **Film Capacitors**: Made from thin plastic films, these capacitors are known for their reliability and are often used in audio and signal processing applications.
B. Applications of Capacitors in Various Industries
Capacitors find applications across multiple industries:
1. **Consumer Electronics**: In devices like smartphones and televisions, capacitors help manage power supply and signal processing.
2. **Automotive**: Capacitors are used in various automotive systems, including power management and audio systems.
3. **Industrial Machinery**: Capacitors play a vital role in motor starting and power factor correction in industrial settings.
4. **Renewable Energy Systems**: In solar inverters and wind turbines, capacitors help stabilize voltage and improve efficiency.
III. Regulatory Bodies and Standards Organizations
A. Overview of Key Organizations
Several organizations are responsible for establishing product standards for capacitors:
1. **International Electrotechnical Commission (IEC)**: The IEC develops international standards for electrical and electronic devices, including capacitors.
2. **Institute of Electrical and Electronics Engineers (IEEE)**: IEEE standards focus on electrical engineering and electronics, providing guidelines for capacitor performance and testing.
3. **Underwriters Laboratories (UL)**: UL is known for its safety certification, ensuring that capacitors meet safety standards for various applications.
4. **American National Standards Institute (ANSI)**: ANSI oversees the development of voluntary consensus standards for products, including capacitors.
B. Role of These Organizations in Setting Standards
These organizations collaborate with industry experts to create and update standards that ensure capacitors are safe, reliable, and effective. Their guidelines cover various aspects, including electrical performance, environmental impact, and safety requirements.
IV. Key Product Standards for Capacitors
A. Electrical Characteristics
1. **Capacitance Tolerance**: This standard specifies the allowable deviation from the nominal capacitance value. It ensures that capacitors perform within acceptable limits in circuits.
2. **Voltage Rating**: Capacitors must be rated for the maximum voltage they can handle without failure. Exceeding this rating can lead to catastrophic failure.
3. **Equivalent Series Resistance (ESR)**: ESR is a measure of the internal resistance of a capacitor, affecting its efficiency and heat generation. Lower ESR values are preferred for high-frequency applications.
4. **Leakage Current**: This standard measures the small amount of current that flows through a capacitor when it is not in use. High leakage current can indicate a failure or degradation of the capacitor.
B. Environmental and Mechanical Standards
1. **Temperature Range**: Capacitors must operate effectively within specified temperature ranges to ensure reliability in various environments.
2. **Humidity Resistance**: Capacitors are tested for their ability to withstand high humidity levels, which can affect their performance and longevity.
3. **Vibration and Shock Resistance**: Capacitors used in automotive and industrial applications must endure mechanical stress without failure.
C. Safety Standards
1. **Fire Safety**: Capacitors must meet fire safety standards to prevent ignition and ensure safe operation in electronic devices.
2. **RoHS Compliance**: The Restriction of Hazardous Substances (RoHS) directive limits the use of specific hazardous materials in electronic products, including capacitors.
3. **REACH Compliance**: The Registration, Evaluation, Authorisation, and Restriction of Chemicals (REACH) regulation ensures that chemicals used in capacitors are safe for human health and the environment.
V. Testing and Certification Processes
A. Overview of Testing Methods
1. **Electrical Testing**: This includes measuring capacitance, ESR, and leakage current to ensure that capacitors meet specified electrical characteristics.
2. **Environmental Testing**: Capacitors undergo tests to evaluate their performance under extreme temperature, humidity, and mechanical stress conditions.
3. **Mechanical Testing**: This involves assessing the physical integrity of capacitors under vibration and shock conditions.
B. Certification Process for Capacitors
1. **Pre-Certification Testing**: Before a capacitor can be certified, it undergoes rigorous testing to ensure it meets all relevant standards.
2. **Compliance Verification**: After testing, manufacturers must provide documentation demonstrating compliance with applicable standards.
3. **Ongoing Quality Assurance**: Manufacturers are required to maintain quality control processes to ensure that all produced capacitors continue to meet established standards.
VI. Challenges in Meeting Product Standards
A. Variability in Manufacturing Processes
Manufacturing processes can vary significantly between different manufacturers, leading to inconsistencies in capacitor performance. This variability can make it challenging to meet established standards consistently.
B. Evolving Technology and Standards
As technology advances, so do the standards governing capacitors. Manufacturers must stay updated on changes to ensure compliance, which can be resource-intensive.
C. Global Market Considerations
With a global market for capacitors, manufacturers must navigate different regulatory requirements in various countries, complicating the compliance process.
VII. Future Trends in Capacitor Standards
A. Innovations in Capacitor Technology
Emerging technologies, such as supercapacitors and organic capacitors, are changing the landscape of energy storage. Standards will need to evolve to accommodate these new technologies.
B. Anticipated Changes in Regulatory Standards
As environmental concerns grow, stricter regulations regarding the materials used in capacitors and their disposal are expected. Manufacturers will need to adapt to these changes to remain compliant.
C. The Impact of Sustainability on Capacitor Design and Standards
Sustainability is becoming a priority in capacitor design, with a focus on reducing environmental impact. Standards will likely evolve to promote the use of eco-friendly materials and manufacturing processes.
VIII. Conclusion
Product standards for capacitors are vital for ensuring their safety, reliability, and performance in electronic circuits. These standards, established by various regulatory bodies, cover electrical characteristics, environmental and mechanical requirements, and safety considerations. As technology evolves and the demand for sustainable practices increases, the standards governing capacitors will continue to adapt. Manufacturers must remain vigilant in meeting these standards to ensure their products are safe and effective in an ever-changing market.
IX. References
- International Electrotechnical Commission (IEC) Standards
- Institute of Electrical and Electronics Engineers (IEEE) Standards
- Underwriters Laboratories (UL) Certification Guidelines
- American National Standards Institute (ANSI) Standards
- RoHS and REACH Compliance Guidelines
This comprehensive overview of product standards for capacitors highlights their critical role in the electronics industry and the ongoing efforts to ensure their safety and effectiveness. As we look to the future, the evolution of these standards will be essential in meeting the challenges posed by new technologies and environmental considerations.