What are the Manufacturing Processes of the Latest Wirewound Resistors?
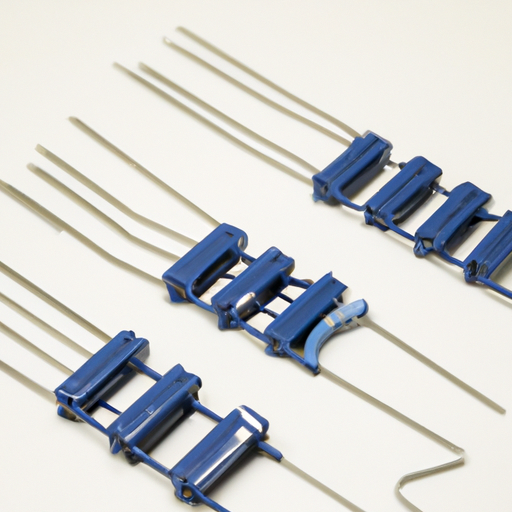
I. Introduction
Wirewound resistors are a crucial component in the world of electronics, known for their precision and reliability. These resistors are constructed by winding a wire around a core, which allows for a high degree of accuracy in resistance values. Their importance spans various applications, from power electronics to telecommunications, making them indispensable in modern circuitry. This blog post will delve into the manufacturing processes of the latest wirewound resistors, exploring the materials used, the steps involved in production, and the innovations shaping their future.
II. Historical Context
Wirewound resistors have a rich history that dates back to the early days of electronics. Initially, these resistors were made using simple materials and rudimentary techniques. Over the decades, advancements in technology and materials have led to significant improvements in their performance and reliability. Compared to other types of resistors, such as carbon and film resistors, wirewound resistors offer superior stability and precision, particularly in high-power applications. The evolution of wirewound resistors reflects broader trends in electronics, where the demand for higher performance and miniaturization drives innovation.
III. Materials Used in Wirewound Resistors
The performance of wirewound resistors is heavily influenced by the materials used in their construction.
A. Types of Wire Materials
1. **Nickel-chromium (NiCr)**: This alloy is commonly used due to its excellent temperature coefficient and resistance to oxidation. NiCr wire is ideal for high-temperature applications, making it a popular choice in industrial settings.
2. **Copper-nickel (CuNi)**: Known for its good conductivity and stability, CuNi wire is often used in applications where lower resistance values are required.
3. **Other Alloys**: Various other alloys may be employed depending on specific application requirements, including those that enhance thermal stability or reduce cost.
B. Insulating Materials
1. **Ceramic**: Ceramic cores are favored for their high thermal resistance and electrical insulation properties. They can withstand high temperatures without degrading.
2. **Epoxy**: Epoxy resins are often used for their excellent adhesion and moisture resistance, providing a protective layer that enhances durability.
3. **Other Composites**: Advanced composite materials are increasingly being used to improve performance and reduce weight.
C. Coating Materials for Protection and Performance
Coatings play a vital role in protecting wirewound resistors from environmental factors. These coatings can enhance thermal stability, moisture resistance, and overall durability, ensuring that the resistors maintain their performance over time.
IV. Manufacturing Processes
The manufacturing of wirewound resistors involves several key processes, each critical to ensuring the final product meets stringent performance standards.
A. Wire Winding
1. **Selection of Wire Gauge and Length**: The first step in manufacturing wirewound resistors is selecting the appropriate wire gauge and length. This choice directly impacts the resistance value and power rating of the resistor.
2. **Winding Techniques**: Wire can be wound manually or through automated processes. Automated winding machines are increasingly common, allowing for greater precision and efficiency.
3. **Layering and Spacing Considerations**: Proper layering and spacing of the wire are essential to prevent short circuits and ensure uniform resistance. Advanced machines can control these parameters with high accuracy.
B. Core Preparation
1. **Types of Cores**: The core material can vary, with options including ceramic and metal. Each type has its advantages, such as thermal stability or conductivity.
2. **Core Shaping and Treatment**: Cores must be shaped and treated to ensure they can withstand the stresses of operation. This may involve processes like sintering for ceramics or surface treatments for metals.
C. Assembly
1. **Joining the Wire to the Terminals**: After winding, the wire must be securely attached to the terminals. This step is crucial for ensuring electrical connectivity and mechanical stability.
2. **Ensuring Electrical and Mechanical Integrity**: The assembly process must guarantee that the resistor can withstand operational stresses without failure. This often involves rigorous testing and quality checks.
D. Insulation and Coating
1. **Application of Insulating Materials**: Insulating materials are applied to prevent electrical shorts and protect the resistor from environmental factors.
2. **Curing Processes for Coatings**: Coatings must be cured properly to achieve their full protective properties. This may involve heat treatment or chemical curing processes.
E. Testing and Quality Control
1. **Electrical Testing**: Each resistor undergoes electrical testing to verify its resistance value and tolerance. This ensures that it meets the specified performance criteria.
2. **Mechanical Testing**: Mechanical tests assess the durability and thermal stability of the resistor, ensuring it can withstand the rigors of its intended application.
3. **Environmental Testing**: Resistors are also subjected to environmental tests, including humidity and temperature cycling, to ensure they perform reliably under various conditions.
V. Innovations in Wirewound Resistor Manufacturing
The manufacturing landscape for wirewound resistors is evolving rapidly, driven by technological advancements.
A. Automation and Robotics in Production
Automation has revolutionized the production of wirewound resistors, allowing for higher precision and reduced labor costs. Robotic systems can perform repetitive tasks with consistent quality, leading to improved efficiency.
B. Advanced Materials and Their Impact on Performance
The development of new materials has enhanced the performance of wirewound resistors. For instance, the use of advanced alloys can improve thermal stability and reduce resistance drift over time.
C. Customization and Precision Engineering
Manufacturers are increasingly offering customized solutions to meet specific customer requirements. Precision engineering techniques allow for the production of resistors tailored to unique applications, enhancing their effectiveness.
D. Sustainability Practices in Manufacturing
As environmental concerns grow, manufacturers are adopting sustainable practices in their production processes. This includes using eco-friendly materials and reducing waste, contributing to a more sustainable electronics industry.
VI. Applications of Wirewound Resistors
Wirewound resistors find applications across various industries, showcasing their versatility and reliability.
A. Use in Power Electronics
In power electronics, wirewound resistors are essential for managing energy flow and ensuring system stability. Their ability to handle high power levels makes them ideal for applications such as power supplies and motor drives.
B. Applications in Automotive and Aerospace Industries
In the automotive and aerospace sectors, wirewound resistors are used in critical systems where reliability is paramount. They are often found in braking systems, engine control units, and avionics.
C. Role in Telecommunications and Data Centers
Wirewound resistors play a vital role in telecommunications and data centers, where they help manage signal integrity and power distribution.
D. Emerging Applications in Renewable Energy Systems
With the rise of renewable energy systems, wirewound resistors are increasingly used in applications such as solar inverters and wind turbine controllers, where their reliability and performance are crucial.
VII. Challenges and Future Trends
Despite their advantages, the manufacturing of wirewound resistors faces several challenges.
A. Challenges in Manufacturing
Cost and scalability remain significant challenges for manufacturers. As demand for high-performance resistors grows, companies must find ways to produce them efficiently without compromising quality.
B. Future Trends in Wirewound Resistor Technology
The future of wirewound resistors is likely to be shaped by advancements in materials science and manufacturing techniques. Innovations such as 3D printing and nanotechnology may lead to new designs and improved performance.
C. Potential Impact of Emerging Technologies
Emerging technologies like AI and IoT are expected to influence the manufacturing processes of wirewound resistors. These technologies can enhance quality control, optimize production processes, and enable real-time monitoring of resistor performance.
VIII. Conclusion
Wirewound resistors are a cornerstone of modern electronics, offering precision and reliability across a wide range of applications. The manufacturing processes behind these components are complex and continually evolving, driven by advancements in materials and technology. As the demand for high-performance resistors grows, manufacturers must adapt to new challenges and embrace innovations that will shape the future of wirewound resistors. Their significance in the electronics industry cannot be overstated, and the outlook for their manufacturing processes and applications remains bright.
IX. References
- Academic journals and articles on resistor technology
- Industry reports and white papers on electronics manufacturing
- Manufacturer specifications and guidelines for wirewound resistors
This comprehensive overview of wirewound resistors and their manufacturing processes highlights the importance of these components in modern electronics and the innovations that continue to drive their development.
What are the Manufacturing Processes of the Latest Wirewound Resistors?
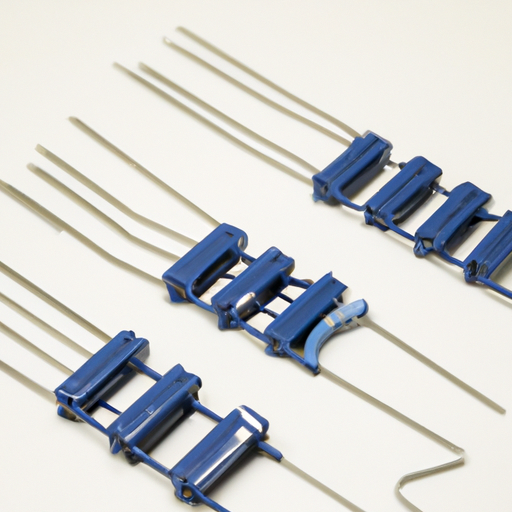
I. Introduction
Wirewound resistors are a crucial component in the world of electronics, known for their precision and reliability. These resistors are constructed by winding a wire around a core, which allows for a high degree of accuracy in resistance values. Their importance spans various applications, from power electronics to telecommunications, making them indispensable in modern circuitry. This blog post will delve into the manufacturing processes of the latest wirewound resistors, exploring the materials used, the steps involved in production, and the innovations shaping their future.
II. Historical Context
Wirewound resistors have a rich history that dates back to the early days of electronics. Initially, these resistors were made using simple materials and rudimentary techniques. Over the decades, advancements in technology and materials have led to significant improvements in their performance and reliability. Compared to other types of resistors, such as carbon and film resistors, wirewound resistors offer superior stability and precision, particularly in high-power applications. The evolution of wirewound resistors reflects broader trends in electronics, where the demand for higher performance and miniaturization drives innovation.
III. Materials Used in Wirewound Resistors
The performance of wirewound resistors is heavily influenced by the materials used in their construction.
A. Types of Wire Materials
1. **Nickel-chromium (NiCr)**: This alloy is commonly used due to its excellent temperature coefficient and resistance to oxidation. NiCr wire is ideal for high-temperature applications, making it a popular choice in industrial settings.
2. **Copper-nickel (CuNi)**: Known for its good conductivity and stability, CuNi wire is often used in applications where lower resistance values are required.
3. **Other Alloys**: Various other alloys may be employed depending on specific application requirements, including those that enhance thermal stability or reduce cost.
B. Insulating Materials
1. **Ceramic**: Ceramic cores are favored for their high thermal resistance and electrical insulation properties. They can withstand high temperatures without degrading.
2. **Epoxy**: Epoxy resins are often used for their excellent adhesion and moisture resistance, providing a protective layer that enhances durability.
3. **Other Composites**: Advanced composite materials are increasingly being used to improve performance and reduce weight.
C. Coating Materials for Protection and Performance
Coatings play a vital role in protecting wirewound resistors from environmental factors. These coatings can enhance thermal stability, moisture resistance, and overall durability, ensuring that the resistors maintain their performance over time.
IV. Manufacturing Processes
The manufacturing of wirewound resistors involves several key processes, each critical to ensuring the final product meets stringent performance standards.
A. Wire Winding
1. **Selection of Wire Gauge and Length**: The first step in manufacturing wirewound resistors is selecting the appropriate wire gauge and length. This choice directly impacts the resistance value and power rating of the resistor.
2. **Winding Techniques**: Wire can be wound manually or through automated processes. Automated winding machines are increasingly common, allowing for greater precision and efficiency.
3. **Layering and Spacing Considerations**: Proper layering and spacing of the wire are essential to prevent short circuits and ensure uniform resistance. Advanced machines can control these parameters with high accuracy.
B. Core Preparation
1. **Types of Cores**: The core material can vary, with options including ceramic and metal. Each type has its advantages, such as thermal stability or conductivity.
2. **Core Shaping and Treatment**: Cores must be shaped and treated to ensure they can withstand the stresses of operation. This may involve processes like sintering for ceramics or surface treatments for metals.
C. Assembly
1. **Joining the Wire to the Terminals**: After winding, the wire must be securely attached to the terminals. This step is crucial for ensuring electrical connectivity and mechanical stability.
2. **Ensuring Electrical and Mechanical Integrity**: The assembly process must guarantee that the resistor can withstand operational stresses without failure. This often involves rigorous testing and quality checks.
D. Insulation and Coating
1. **Application of Insulating Materials**: Insulating materials are applied to prevent electrical shorts and protect the resistor from environmental factors.
2. **Curing Processes for Coatings**: Coatings must be cured properly to achieve their full protective properties. This may involve heat treatment or chemical curing processes.
E. Testing and Quality Control
1. **Electrical Testing**: Each resistor undergoes electrical testing to verify its resistance value and tolerance. This ensures that it meets the specified performance criteria.
2. **Mechanical Testing**: Mechanical tests assess the durability and thermal stability of the resistor, ensuring it can withstand the rigors of its intended application.
3. **Environmental Testing**: Resistors are also subjected to environmental tests, including humidity and temperature cycling, to ensure they perform reliably under various conditions.
V. Innovations in Wirewound Resistor Manufacturing
The manufacturing landscape for wirewound resistors is evolving rapidly, driven by technological advancements.
A. Automation and Robotics in Production
Automation has revolutionized the production of wirewound resistors, allowing for higher precision and reduced labor costs. Robotic systems can perform repetitive tasks with consistent quality, leading to improved efficiency.
B. Advanced Materials and Their Impact on Performance
The development of new materials has enhanced the performance of wirewound resistors. For instance, the use of advanced alloys can improve thermal stability and reduce resistance drift over time.
C. Customization and Precision Engineering
Manufacturers are increasingly offering customized solutions to meet specific customer requirements. Precision engineering techniques allow for the production of resistors tailored to unique applications, enhancing their effectiveness.
D. Sustainability Practices in Manufacturing
As environmental concerns grow, manufacturers are adopting sustainable practices in their production processes. This includes using eco-friendly materials and reducing waste, contributing to a more sustainable electronics industry.
VI. Applications of Wirewound Resistors
Wirewound resistors find applications across various industries, showcasing their versatility and reliability.
A. Use in Power Electronics
In power electronics, wirewound resistors are essential for managing energy flow and ensuring system stability. Their ability to handle high power levels makes them ideal for applications such as power supplies and motor drives.
B. Applications in Automotive and Aerospace Industries
In the automotive and aerospace sectors, wirewound resistors are used in critical systems where reliability is paramount. They are often found in braking systems, engine control units, and avionics.
C. Role in Telecommunications and Data Centers
Wirewound resistors play a vital role in telecommunications and data centers, where they help manage signal integrity and power distribution.
D. Emerging Applications in Renewable Energy Systems
With the rise of renewable energy systems, wirewound resistors are increasingly used in applications such as solar inverters and wind turbine controllers, where their reliability and performance are crucial.
VII. Challenges and Future Trends
Despite their advantages, the manufacturing of wirewound resistors faces several challenges.
A. Challenges in Manufacturing
Cost and scalability remain significant challenges for manufacturers. As demand for high-performance resistors grows, companies must find ways to produce them efficiently without compromising quality.
B. Future Trends in Wirewound Resistor Technology
The future of wirewound resistors is likely to be shaped by advancements in materials science and manufacturing techniques. Innovations such as 3D printing and nanotechnology may lead to new designs and improved performance.
C. Potential Impact of Emerging Technologies
Emerging technologies like AI and IoT are expected to influence the manufacturing processes of wirewound resistors. These technologies can enhance quality control, optimize production processes, and enable real-time monitoring of resistor performance.
VIII. Conclusion
Wirewound resistors are a cornerstone of modern electronics, offering precision and reliability across a wide range of applications. The manufacturing processes behind these components are complex and continually evolving, driven by advancements in materials and technology. As the demand for high-performance resistors grows, manufacturers must adapt to new challenges and embrace innovations that will shape the future of wirewound resistors. Their significance in the electronics industry cannot be overstated, and the outlook for their manufacturing processes and applications remains bright.
IX. References
- Academic journals and articles on resistor technology
- Industry reports and white papers on electronics manufacturing
- Manufacturer specifications and guidelines for wirewound resistors
This comprehensive overview of wirewound resistors and their manufacturing processes highlights the importance of these components in modern electronics and the innovations that continue to drive their development.